-
Aluminum Alloy Casting
-
Pressure Die Casting Mould
-
Metal Casting Molds
-
Aluminium Die Casting Mould
-
EPS Foam Mould
-
Lost Foam Mould
-
Sand Casting Mould
-
Permanent Mold Casting Aluminum
-
Aluminium Gravity Die Casting
-
Die Cast Aluminum Tooling
-
Auto Parts Mould
-
Multi Cavity Mold
-
Cylinder Head Mold
-
High Precision Mold
-
Rapid 3d Printing Service
-
Greg HenkThanks for your kindly hospitality. Your company is very professional , we will have nice cooperation in the near future.
-
Lionel LoboGood company with nice service and high quality and high reputation. One of our reliable supplier , goods are delivered in time and nice package.
Oem Pressure Die Casting Mould Engine Components Transmission Cases
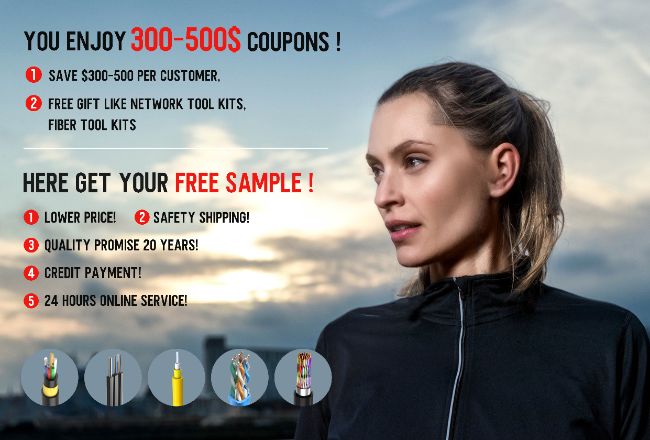
Contact me for free samples and coupons.
WhatsApp:0086 18588475571
Wechat: 0086 18588475571
Skype: sales10@aixton.com
If you have any concern, we provide 24-hour online help.
xProduct Name | OEM Pressure Die Casting Mould | Product Material | ADC12 ADC10 |
---|---|---|---|
Usage | Engine Components Transmission Cases | Average Wall Thickness | >3mm |
Demoulding | Automatic | Mould Life | 500,000-1,000,000 Shots |
Using Hardness | >HRC45 | ||
Highlight | oem pressure die casting mould,transmission cases pressure die casting mould,oem high pressure die casting mold |
OEM Pressure Die Casting Mould Engine Components Transmission Cases
Aluminium die casting offers several advantages, including:
-
Lightweight: Aluminium is known for its low density, making it an ideal choice for producing lightweight products with high strength.
-
High dimensional accuracy: Die casting ensures precise and consistent dimensions, resulting in products with tight tolerances and minimal variations.
-
Complex shapes: The die casting process allows for intricate and complex designs to be created, enabling the production of products with intricate details and features.
-
Excellent surface finish: Aluminium die casting provides a smooth and aesthetically pleasing surface finish, reducing the need for additional finishing operations.
Pressure Die Casting Mould Description
Specification | Customized,customer required,customer's drawings |
Material | ADC12/ADC10/A380/A383/A390/413/AllSi9Cu3/AlSi10Mg,etc. |
Application |
Automobile, agricultural machinery, furniture, construction, home appliances, electronics. |
Process | High pressure die casting or Semi-solid thixoforming |
Machining | CNC machining center, CNC lathe |
Casting tolerance | IT4 - IT6 |
Machining tolerance | +/- 0.005mm,ISO2768-f |
Standard | DIN,ASTM,GOST,ISO,BS |
Heat treatment | Annealing treatment,solution treatment ,T1,T2,T3,T4,T5,T6 |
Unit weight | 5g-30kg |
Dimensions | <=1500mm |
Die casting machine specification | 150T-3000T |
Certificate | ISO9001, TS16949,ISO1400,RoHS |
Finish | Plating,Painting,Powder Coating,Polishing, Stoving Varnish,Anodizing |
Quality control | FEMA,PPAP,APQP,Control Plan,MSA, Certificates for all requirements Test reports for every delivery |
Service | Weekly report,Key node report,Any questions will be answered within 24 hours. |
Manufacture Process
1. Review the part design,drawings and quality standard from clients.
2. Mould and Tooling design & manufacturing
3. Mould and Tooling testing & confirm the sample
4. Die casting raw castings
5. Surface treatment: Trimming,Deburring, polishing, cleaning, passivation & power coating and other requirement from Customer
6. Precision machining: CNC lathes, milling, drilling, grinding etc
7. Full Inspection
8. Packing
9. Delivery
Our Advantages
1. We are the biggest lost foam mould manufacturer in China, we focus on high challenge lost foam mould and we have large gantry machining centers,30 sets imported high speed machining center,more than 40 sets general machine tool equipment;
2. We have 36 senior mould designers, to ensure reasonable / safety / high efficiency mould design and ensure the fast mould delivery and rational mould structure, make the process more safer and the production efficiency more higher;
3. We using numerical control machine tool to manufacture the mould cavities, to ensure a even thickness ;
4. We using ZL104 Aluminium to casting the mould, to manufacture a high strength mould;
5. For the big mould, we using Ø22*1 copper tube as cooling pipe, with water spray system, to get a nice cooling effect;
6. We Have (TEF10N) coating on the mould surface, it can reduce the friction, anti water/static electricity/acid-base/high-temperature, with this we can ensure the pattern has smooth surface without distrotion, and easy to demould;
7. All the screws we using stainless steel screw, easy to disassemble during maintenance;
8. For the big mould chest, we using 18-20mm thick wrought aluminium plate, to offer high strenght cavity ;
9. For the complex mould which is difficult to demould, we can manufacture the automaitc mould with take out device ;
10. We produce the pattern sample to customer after finish the mould, when the pattern was qualified, then we do exceptance job for the mould ;
11. We have the Hexagon coordinate measuring instrument imported from the Switzerland to have a test make sure our mould qualified.
Company profile
Luoyang Liushi mould Co., Ltd was established on 2001, which is National Standard Setting Unit for Lost Foam Casting Mould. The company is located in the Millennium Emperor, peony flower city of Luoyang City. We have 9800 office building, and 22000 workshop, which is well equipped with research, development, design, foundry, machining, assembly, surface treatment and other equipment. It′s a Luoyang municipal R&D center and technology center.
Company technicians can provide on-site guide mould assembly, test production, free repair and complete technology for lost foam casting proecss according to customer demands. With the business philosophy of "careful design, lean manufacture, best service, perfect quality", we strive to provide satisfactory products and services for customers. After years of development, our company has become the preferred mould suppliers of many lost foam casting manufacturers and the exclusive supplier.