-
Aluminum Alloy Casting
-
Pressure Die Casting Mould
-
Metal Casting Molds
-
Aluminium Die Casting Mould
-
EPS Foam Mould
-
Lost Foam Mould
-
Sand Casting Mould
-
Permanent Mold Casting Aluminum
-
Aluminium Gravity Die Casting
-
Die Cast Aluminum Tooling
-
Auto Parts Mould
-
Multi Cavity Mold
-
Cylinder Head Mold
-
High Precision Mold
-
Rapid 3d Printing Service
-
Greg HenkThanks for your kindly hospitality. Your company is very professional , we will have nice cooperation in the near future.
-
Lionel LoboGood company with nice service and high quality and high reputation. One of our reliable supplier , goods are delivered in time and nice package.
Car Parts Mould Design Maker Customize Service Auto Parts ABS High Precision Molding
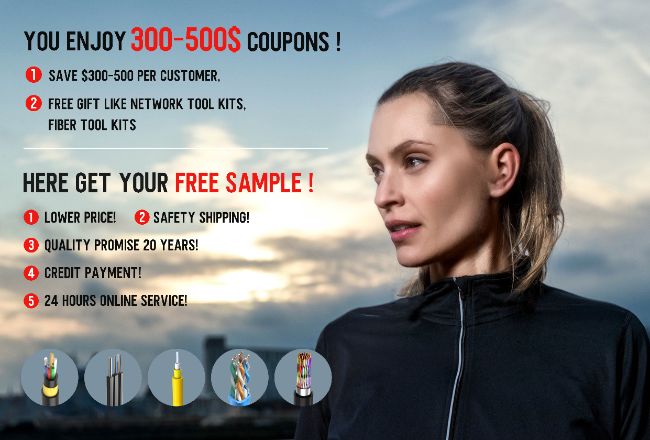
Contact me for free samples and coupons.
WhatsApp:0086 18588475571
Wechat: 0086 18588475571
Skype: sales10@aixton.com
If you have any concern, we provide 24-hour online help.
xCasting Method | Casting | Tolerance | ±0.1mm-±0.5mm |
---|---|---|---|
Drawing Format | PDF, DWG, IGS, STP, Etc. | Size | Customized |
Processing Technology | CNC Machining, Drilling, Milling, Turning, Etc. | Packaging | Wooden Cases, Cartons, Pallets, Etc. |
Material | Aluminum Alloy | Feature | Durability & Longevity |
Highlight | Car Parts Mould Design Maker,ABS High Precision Auto Parts Mould,Customize Service Auto Parts Mould |
Car Parts Mould Design Maker Customize Service ABS High Precision Molding
Product Description:
Unlock the full potential of your automotive manufacturing with our 'Custom Car Parts Mould Design and High Precision Molding Service'. Specializing in aluminum tooling, we offer end-to-end solutions for designing and producing high-performance molds tailored to your specific requirements. Whether you need molds for exterior panels, interior trim, or structural components, our team leverages advanced technologies and precision machining to deliver molds that meet the highest standards of accuracy, durability, and efficiency. Ideal for OEMs, Tier 1 suppliers, and aftermarket manufacturers, our service ensures seamless integration into your production line while reducing costs and lead times.

Features:
- Customized OEM Solutions - Tailored designs to meet your exact specifications for motor housings, pump casings, and engine components. - Supports complex geometries, cooling fins, and integrated mounting points.
- High-Performance Aluminum Alloys - Excellent thermal conductivity for efficient heat dissipation in high-power motors.
- Precision Die Casting Technology- High-pressure die casting (HPDC) ensures tight tolerances (±0.04mm) and consistent quality. - Smooth surface finishes (Ra ≤ 0.4μm) for reduced post-processing and enhanced aesthetics. environmental impact.
- Fast Turnaround & Scalability - Rapid prototyping and production-ready molds delivered within 5–7 weeks. - Scalable solutions for low to high-volume production runs.
Technical Parameters:
Parameter | Value |
---|---|
Heat Treatment | Annealing, Quenching, Tempering, Etc. |
Surface Treatment | Polishing, Sandblasting, Anodizing, Etc. |
Processing Technology | CNC Machining, Drilling, Milling, Turning, Etc. |
Material | Aluminum Alloy |
Casting Method | Casting |
Inspection | 100% Inspection |
Packaging | Wooden Cases, Cartons, Pallets, Etc. |
Application | Automotive |
Tolerance | ±0.1mm-±0.5mm |
Drawing Format | PDF, DWG, IGS, STP, Etc. |
Manufacture Process:
1. Review the part design,drawings and quality standard from clients.
2. Mould and Tooling design & manufacturing
3. Mould and Tooling testing & confirm the sample
4. Die casting raw castings
5. Surface treatment: Trimming,Deburring, polishing, cleaning, passivation & power coating and other requirement from Customer
6. Precision machining: CNC lathes, milling, drilling, grinding etc
7. Full Inspection
8. Packing
9. Delivery
Our Advantages
1. We are the biggest lost foam mould manufacturer in China, we focus on high challenge lost foam mould and we have large gantry machining centers,30 sets imported high speed machining center,more than 40 sets general machine tool equipment;
2. We have 36 senior mould designers, to ensure reasonable / safety / high efficiency mould design and ensure the fast mould delivery and rational mould structure, make the process more safer and the production efficiency more higher;
3. We using numerical control machine tool to manufacture the mould cavities, to ensure a even thickness ;
4. We using ZL104 Aluminium to casting the mould, to manufacture a high strength mould;
5. For the big mould, we using Ø22*1 copper tube as cooling pipe, with water spray system, to get a nice cooling effect;
6. We Have (TEF10N) coating on the mould surface, it can reduce the friction, anti water/static electricity/acid-base/high-temperature, with this we can ensure the pattern has smooth surface without distrotion, and easy to demould;
7. All the screws we using stainless steel screw, easy to disassemble during maintenance;
8. For the big mould chest, we using 18-20mm thick wrought aluminium plate, to offer high strenght cavity.